Choosing the right material for fasteners is a strategic decision that directly impacts the safety, performance and durability of any industrial installation. Although galvanised steel, carbon steel or aluminium are still used in many environments, stainless fasteners have established themselves as one of the most balanced options, especially when looking for long-term reliability and resistance to adverse conditions.
In this article we analyse the main differences between these options and help you to identify which is the most suitable depending on the environment of use.
Corrosion resistance
One of the most significant differences between the materials used in fasteners is their resistance to corrosion. Stainless steel fasteners, especially in A2 and A4 grades, stand out for their excellent performance in humid, marine or chemical environments. In outdoor applications, such as urban metal structures, solar installations or maritime elements, the use of stainless steel guarantees long-lasting protection without the need for additional coatings.
Galvanised steel, on the other hand, offers good initial resistance due to its zinc coating, but may deteriorate over time if the surface layer is damaged, especially in coastal areas or when exposed to chemicals. Aluminium, on the other hand, is susceptible to galvanic corrosion when in contact with other metals and therefore requires additional precautions in its installation.
Therefore, when the environment involves constant exposure to moisture, salt spray or chemicals, A4 stainless steel is the more reliable and durable choice.
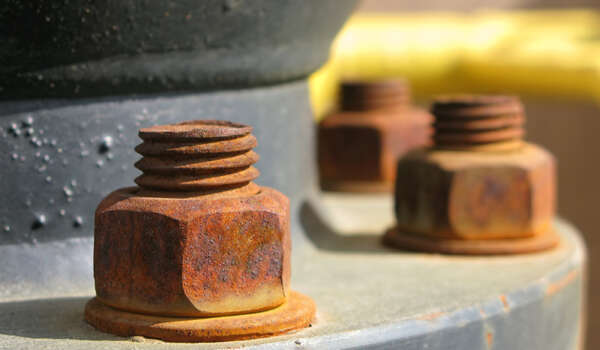
Mechanical strength and structural behaviour
From a mechanical strength point of view, carbon steel in grades 8.8 or 10.9 remains the reference for applications requiring high loads or dynamic stresses, such as heavy machinery, steel structures or bridges.
However, stainless steel in grades A2-70 or A4-80 offers a competitive balance between mechanical strength and corrosion performance, being perfectly suitable for most medium-load industrial and structural assemblies.
Aluminium, on the other hand, has significantly lower strength and is therefore usually reserved for lightweight applications where weight is a key factor, such as in the manufacture of bodywork, ancillary structures or non-stressed parts.
In short, if structural loading is the primary objective, carbon steel may be preferable. But if you are looking for a versatile material that is both load bearing and corrosion resistant, stainless steel is the more efficient choice.
Maintenance, durability and service life
One of the great advantages of stainless steel fasteners is their minimum maintenance. No coatings, periodic inspections or additional treatments are required, which translates into lower operating costs and a longer service life. This is especially important in environments where maintenance access is difficult or where the costs associated with downtime are high.
In contrast, galvanised fasteners require stricter monitoring. Over time, zinc can become less effective and corrosion can occur, especially if there are knocks or wear on the parts. As for aluminium, although it does not rust like steel, its structural deterioration under certain conditions can compromise its prolonged use.
For all these reasons, stainless fasteners offer a more solid return on investment, especially in long-term installations or in demanding environments.
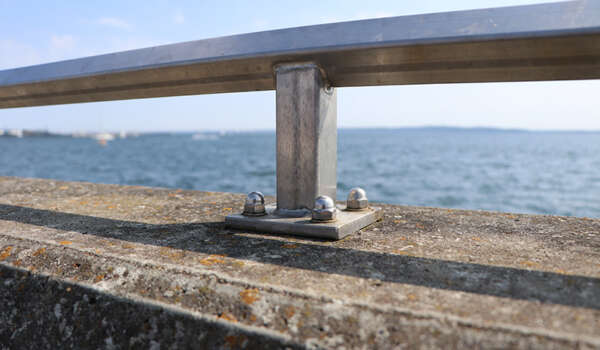
Initial cost vs. long-term profitability
It is true that the initial cost of stainless steel fasteners is higher than other alternatives such as galvanised or aluminium. However, if we analyse its performance over time – its lower maintenance requirements, durability and reliability – it is more cost-effective for most industrial projects.
For temporary or low-budget projects, galvanised steel can meet the basic requirements. But in projects where quality, safety and durability are essential – such as in the food, rail, solar energy or maritime industries – stainless steel is not only recommended, but necessary.
Each material has its place and its use in the industrial world. However, stainless fasteners stand out for their ability to combine mechanical strength, corrosion protection, durability and low maintenance. It is a balanced solution for those seeking reliability and efficiency, especially in sectors where technical and environmental requirements are high.
At CHAVESBAO, we have a complete range of A2 and A4 stainless steel fasteners, as well as solutions in carbon steel and special coatings, so that you can choose the most suitable material depending on your application and environment. Our technical team is available to help you evaluate the best option for your specific project requirements.
Want to know which material is best suited to your application? Contact our specialists.